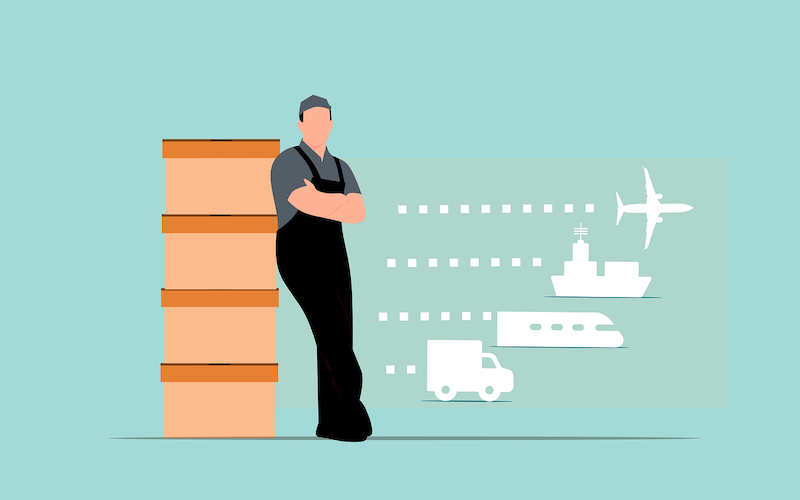
The electronics supply chain has faced big challenges in the last two years. Shortages, delays, and high costs hit many sectors such as automotive, electronics, and telecoms, with COVID-19 exposing weaknesses in the supply chain.
Every shipment delay and slowdown has given companies reason to reconsider their strategies, prompting reassessments and valuable insights for strengthening supply chains in future projects. Here, we share several key lessons learned and solutions from major companies.
Strengthening Supplier Links
One major lesson learned is the importance of forming strong ties with suppliers. For example, a lack of vital electronic parts, like the AMD chipset, can stop the whole production process within a company. However, a shortage doesn’t mean something has disappeared entirely, and businesses with good supplier relationships have an advantage in securing these parts.
Truth is, when demand is high and stock is low, suppliers favor trusted clients. A solid relationship boosts your chances of getting the necessary parts. During the chip shortage, distributors with good connections had better access, while weaker bonds meant business trouble.
Building strong relationships with suppliers calls for open dialogue, honesty, and adaptability. Companies that engaged with suppliers, understood their limits, and worked together, performed better during the shortage crisis. So, the lesson learned here, is that a strong supplier partnership is now essential in this uncertain market.
Broadening Supplier Options
Another takeaway is the importance of fostering relationships with multiple suppliers. As a big company, having only one supplier is borderline risky. What if a hitch happens? No matter if it’s a political or a natural one, it can mean you’re not getting the parts you need anytime soon.
This risk is mitigated by working with many suppliers. By opting for different suppliers, who are preferably situated throughout the state, you’re decreasing the chances of not getting your supplies on time. If a certain supplier faces shortages or decides to go to a halt, you’ll contact your other suppliers to ship you the products. This way, you’re letting syndicates and the state worry about strikes, while you continue working without obstacles.
It’s important to know that different suppliers have different work cultures, which is why you need to be flexible enough to form strong bonds with all of them. Moreover, not every supplier provides the same quality of products and service, which is something you should look past, especially in times of shortage.
Enhancing Inventory Strategies
Good inventory control is crucial for electronics-dependent firms; recent supply management issues highlighted its importance. Companies with just-in-time (JIT) inventory faced unmet demand when supply chains faltered. As much as JIT can cut down costs, it also allows little margin for supply gaps.
The final lesson here is to move towards flexible stock models, mixing both efficiency and risk control. Consider investing in AI tools, as they provide exceptional predictive capabilities. When there is the possibility of a shortage, AI will alert you and allow you to stockpile parts before going through a crisis situation. This way, shortages won’t pose as many obstacles to business continuity as previously anticipated.
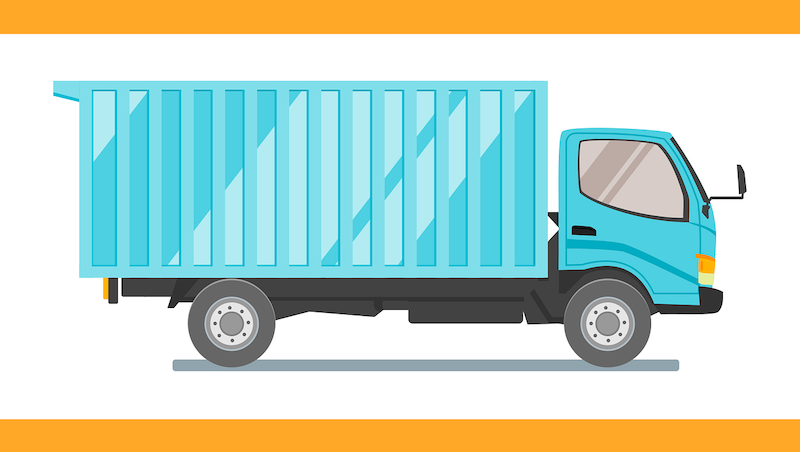
Investing in Local Production
Relying on global chains is a double-edged sword. While it truly helps your business cut down on costs, it also risks disruptions. Because of this, firms are increasingly considering going local when it comes to both sourcing and manufacturing.
Going local offers major benefits over choosing global suppliers, and there are several reasons behind this, including shipping without delays, high tariffs, or political involvement. Furthermore, local production allows faster delivery times, superior quality control measures, and responsive services.
This local shift isn’t about completely abandoning global chains but finding the right balance. You can still have global suppliers, as they can be more affordable, however, building local relationships will prove itself valuable in times of crisis; and you don’t want to be the business owner who wasn’t supporting local suppliers and manufacturers.
Focusing on Sustainability and Openness
Lastly, a key takeaway is the rising value of sustainability and openness. Consumers and regulators want businesses to consider the environmental effects of their supply chains.
Transparently providing insights on component sourcing, manufacturing, and labor conditions builds trust. During global issues, firms open about their struggles and solutions gained more support.
Eco-friendly moves, like recycling and lowering carbon footprints, lead to savings and better chain efficiency. Many firms now integrate these goals for long-term success.
Bottom Line
If anything good came out of the global supply chain disruption, is that companies learned some valuable lessons. Hopefully, business owners will form better connections with local and global suppliers in the future, as it is the only way for their business to thrive, no matter the outside factors. The electronics supply chain management longs for fundamental changes, but taking it one step at a time, companies have a bright future ahead.
Image Source: Pixabay